Undercarriage Wear & Tear: How to Extend the Life of Your Construction Equipment
Learn how to extend the life of your construction equipment undercarriage with proper maintenance. With expert tips, reduce wear and tear on track shoes, sprockets, and rollers.
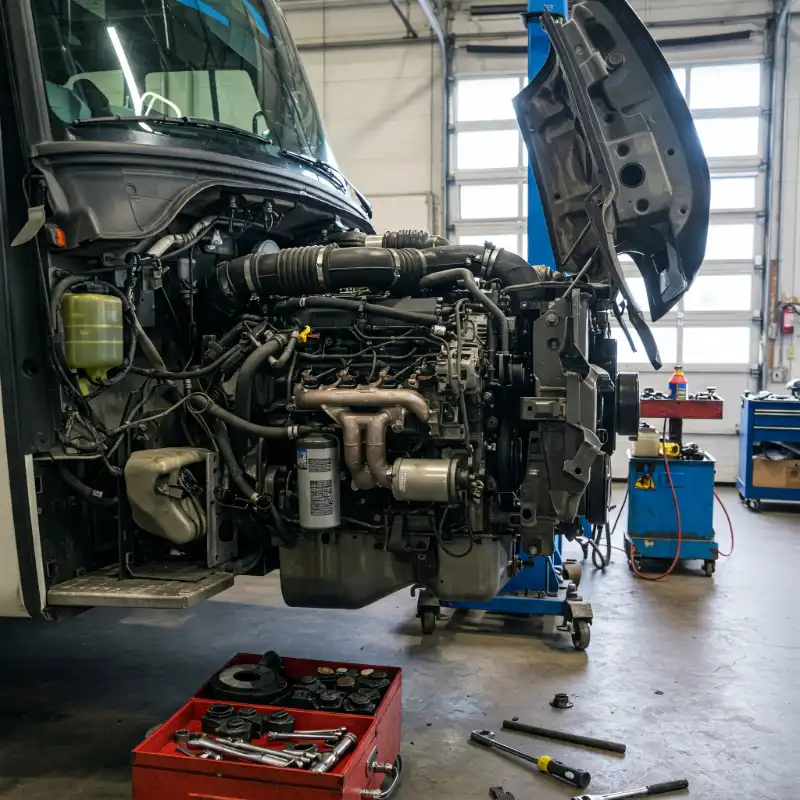
The undercarriage of your construction equipment is the backbone of your machine. It supports the entire weight, handles extreme working conditions, and endures constant abrasion from dirt, rocks, and debris. The undercarriage can quickly wear out if neglected, leading to costly downtime and repairs.
Since undercarriage maintenance can account for nearly 50% of total maintenance costs, extending the lifespan is a top priority for equipment owners and fleet managers. In this guide, we’ll break down common causes of undercarriage wear, maintenance best practices, and cost-saving strategies to keep your equipment running efficiently.
Understanding Undercarriage Wear & Tear
Before discussing maintenance strategies, it’s crucial to understand what contributes to undercarriage deterioration. Knowing these factors allows you to take proactive steps to reduce wear and increase your equipment’s longevity.
1. Terrain & Environmental Conditions
The terrain where construction equipment operates significantly impacts the lifespan of undercarriage components. Rocky terrain causes impact damage, muddy/sandy conditions increase resistance and abrasion, gravel/hard surfaces lead to faster wear, and sloped terrain creates uneven loading. Understanding these challenges helps mitigate wear through adjusted techniques, proper component selection, and regular maintenance.
2. Operating Conditions & Techniques
Various worksite conditions and operating habits can accelerate wear on construction equipment undercarriages. High-speed travel, excessive counter-rotation, frequent inclines with heavy loads, abrasive and rocky terrain, wet and muddy conditions, and lack of maintenance all contribute to premature wear and damage. These factors increase friction, stress, and corrosion, affecting track links, pins, bushings, rollers, and drive sprockets.
3. Improper Track Tension
Proper track tension is crucial for undercarriage longevity in construction equipment. Over-tightened tracks cause excessive wear on rollers, sprockets, and idlers, while loose tracks lead to slippage, de-tracking, and uneven wear. Consulting the operator's manual and regular adjustments are essential for maintaining optimal track tension and preventing damage and safety risks.
Essential Maintenance Tips to Extend Undercarriage Life
Now that you know what causes undercarriage wear, let’s explore practical steps you can take to extend its lifespan.
1. Keep the Undercarriage Clean
To ensure the longevity and efficient operation of construction equipment, a consistent undercarriage cleaning schedule is essential. Daily cleaning after each shift with tools like a pressure washer or air hose prevents debris buildup. Focused cleaning on sprockets, rollers, and track chains is crucial, especially in winter to avoid ice formation. Inspections for wear, use of appropriate cleaning tools, environmental consciousness, and safety precautions like PPE are important. These practices significantly extend undercarriage life and minimize downtime.
2. Inspect the Undercarriage Daily
Regular undercarriage inspections are crucial for preventing costly repairs and extending equipment life. Key areas to inspect include track shoes (for cracks, missing bolts, and wear), sprockets and rollers (for worn teeth, cracks, and leaks), pins and bushings (for seized pins, wear, and elongation), and idlers and track links (for lubrication and alignment). Proactive maintenance is more cost-effective than reactive repairs.
3. Maintain Proper Track Tension
Maintaining proper track tension is crucial for avoiding premature wear, decreased productivity, and increased fuel consumption. Regular checks before each shift, following the manufacturer's recommendations, and adjusting for operating conditions are essential. Track tension is typically adjusted with a grease gun and track adjuster. Consider weather changes and ensure even tension between tracks. If unsure, seek professional maintenance.
4. Rotate Track Pins & Bushings
Track pins and bushings are essential components of the undercarriage system and experience uneven wear over time. To extend their lifespan and optimize track life, it is recommended to perform a bushing turn every 1,000 to 2,000 hours of operation. This process involves rotating the bushing to expose a fresh wear surface, ensuring even wear distribution and preventing premature failure.
Track Rebuild vs. Full Replacement
If the bushings show signs of excessive wear during inspection, it may be more cost-effective to consider a track rebuild instead of a complete track replacement. A track rebuild involves replacing worn bushings and other damaged components, restoring the track to near-new condition, and extending its service life. This option can save significant costs compared to a complete replacement while maintaining the undercarriage's performance.
Addressing Seized Pins
Seized pins are a serious issue that requires immediate attention. When a pin seizes, it prevents the track from articulating smoothly, causing misalignment and increased wear on adjacent components, such as sprockets and rollers. This can lead to premature failure and costly downtime. Addressing seized pins promptly by freeing or replacing them can prevent further damage and ensure the undercarriage's proper functioning.
5. Reduce High-Impact Wear
Optimizing construction equipment undercarriage life involves avoiding counter-rotations, minimizing high-speed travel, and balancing loads evenly. These techniques reduce stress on components, minimize wear, decrease maintenance costs, and improve productivity.
When to Replace Undercarriage Components
Even with meticulous maintenance, undercarriage components will eventually wear out. Ignoring warning signs can lead to catastrophic failures and safety hazards. Signs it’s time to replace components:
- Track Shoes: Excessive wear, loss of traction, or severe gashes.
- Sprockets: Sharp, pointed teeth instead of rounded ones indicate worn sprockets.
- Rollers & Idlers: Rollers that no longer spin freely or have visible cracks and leaks.
- Track Chain Elongation: Excessive stretching that compromises stability.
If you notice these issues, don’t wait for failure—proactive replacements save money and prevent costly downtime.
Cost-Saving Strategies for Undercarriage Maintenance
Since undercarriage repairs are among the most expensive construction equipment maintenance costs, implementing cost-saving strategies is essential.
1. Invest in High-Quality Parts
Cheap, low-quality undercarriage components wear out faster, leading to higher long-term costs.
- Stick to OEM or high-quality aftermarket parts that meet manufacturer specifications.
- Choose track shoes, rollers, and sprockets made from durable, wear-resistant materials.
2. Use Track Guards & Rock Deflectors
Installing track guards and rock deflectors helps prevent debris from damaging undercarriage components.
- Track guards protect rollers and idlers from excessive wear.
- Rock deflectors reduce impact from loose debris, extending the life of track links and shoes.
3. Train Operators on Proper Techniques
Operator behavior significantly impacts undercarriage wear and tear. Training your team on best operating practices can dramatically extend component lifespan.
- Teach operators to avoid excessive counter-rotation and aggressive turning.
- Encourage proper track tensioning and routine undercarriage cleaning.
- Emphasize the importance of balanced loads and careful maneuvering on rough terrain.
4. Implement a Preventive Maintenance Program
Routine preventive maintenance reduces the likelihood of unexpected breakdowns.
- Schedule regular inspections and servicing based on equipment usage hours.
- Keep maintenance logs to track wear patterns and potential problem areas.
- Work with a trusted fleet maintenance provider to ensure thorough, professional undercarriage care.
Final Thoughts
Your construction equipment undercarriage is a significant investment. Proper maintenance and smart operating techniques are essential to protecting it, maximizing efficiency, and reducing costs.
By keeping the undercarriage clean, maintaining track tension, inspecting components daily, and training operators on best practices, you can significantly extend the lifespan of your fleet’s undercarriage components.
Take action today—implement these maintenance strategies and keep your construction fleet running at peak performance!
Shop Locations
Fleetworks Inc. is proud to have expanded to three locations across California, providing a wide-range of truck & equipment repair & fleet services from our locations in Oakland, Santa Fe Springs, Riverside, & the surrounding areas.
Santa Fe Springs Location
14011 Marquardt Ave, Santa Fe Springs, CA 90670
Riverside Location
*Equipment Service & Repairs only*
1310 Dodson Way, Riverside CA, 92507