Hydraulic System Failures in Tractors: Diagnosis and Repair Tips
Learn how to diagnose and repair common tractor hydraulic system failures. Get expert troubleshooting tips to prevent pressure loss, leaks, overheating, and pump failures.
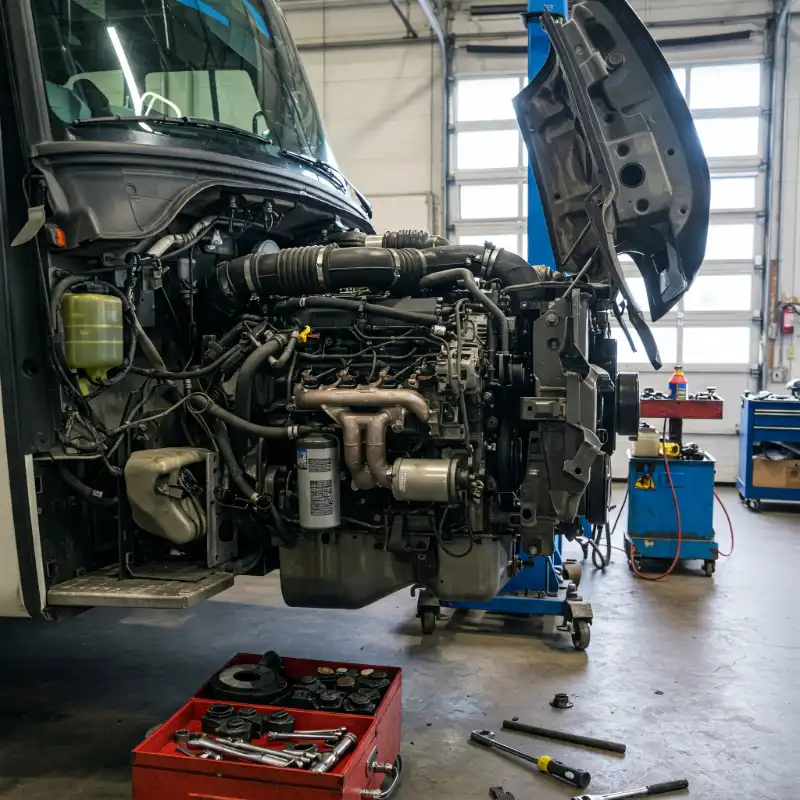
A tractor’s hydraulic system is the backbone of its lifting, steering, and braking operations. When it fails, productivity grinds to a halt. These failures can stem from fluid contamination, pump issues, valve malfunctions, and leaks, among other problems. Understanding the common failure points, diagnosing them correctly, and applying the right repair strategies can keep your tractor running smoothly.
This guide will explain the most common hydraulic failures, their symptoms, and practical repair tips to get your tractor back in the field.
Understanding Hydraulic Systems in Tractors
Before discussing common failures, it’s essential to understand how hydraulic systems work in tractors. These systems operate based on Pascal’s Law, which states that pressure applied to a confined fluid is transmitted equally in all directions. In tractors, this principle powers implements, steering, braking, and lifting.
Key Hydraulic Components:
- Hydraulic Pump – Pressurizes the fluid to power the system.
- Hydraulic Fluid – This transmits force while lubricating and cooling components.
- Control Valves – Regulate fluid flow to different parts of the system.
- Hydraulic Cylinders – Convert hydraulic pressure into mechanical force.
- Filters and Screens – Keep contaminants out of the system.
- Hoses and Fittings – Transport hydraulic fluid to different components.
Now that we have a basic understanding, let’s look at tractors' most common hydraulic failures.
Common Hydraulic System Failures in Tractors
1. Low Hydraulic Pressure
When a tractor’s hydraulic pressure drops, performance suffers. The lift arms may not raise properly, steering becomes sluggish, and attachments lose power.
Causes:
- Worn hydraulic pump – A pump nearing the end of its lifespan may struggle to maintain pressure.
- Clogged filters or screens – Contaminants restrict fluid flow, reducing pressure.
- Leaking seals or hoses – Hydraulic fluid loss results in pressure drops.
- Stuck or damaged pressure relief valve – Prevents the system from maintaining adequate pressure.
Diagnosis and Repair:
- Check hydraulic fluid levels and refill if low.
- Inspect for leaks in hoses, seals, and fittings. Replace damaged components.
- Examine the hydraulic pump for wear or internal damage.
- Test the pressure relief valve and replace it if it’s malfunctioning.
2. Slow or Weak Hydraulic Response
If your tractor's hydraulic loader or three-point hitch moves sluggishly, the system isn't fully operational.
Causes:
- Air in the system – Causes sluggish movement and erratic operation.
- Dirty hydraulic oil – Reduces lubrication and efficiency.
- Blocked suction screen or return filter – Restricts fluid flow.
- Worn or incorrect hydraulic fluid – Reduces performance.
Diagnosis and Repair:
- Bleed the system to remove trapped air.
- Change the hydraulic fluid if it’s contaminated or degraded.
- Clean or replace filters and screens to improve fluid flow.
- Use the correct hydraulic oil recommended by the manufacturer.
3. Overheating Hydraulic System
A tractor’s hydraulic system should operate within an optimal temperature range (100°F–180°F). Seals, hoses, and metal components can be damaged if they overheat.
Causes:
- Low hydraulic fluid levels – Less fluid means less heat dissipation.
- A blocked or dirty cooling system – Prevents proper heat exchange.
- Worn or overworked pump – Generates excessive heat.
- High ambient temperature and heavy load operation – Increases system strain.
Diagnosis and Repair:
- Check fluid levels and top up if necessary.
- Inspect the cooling system, including radiators and fans, for blockages.
- Replace a failing pump to prevent excessive heat buildup.
- Use high-quality hydraulic fluid that meets the tractor’s requirements.
4. Hydraulic Pump Failure
A faulty hydraulic pump leads to a complete loss of hydraulic power, which affects steering, lifting, and braking functions.
Causes:
- Air ingestion (cavitation) – This creates bubbles that damage the pump.
- Worn pump components – Reduces efficiency and pressure.
- Contaminated hydraulic fluid – Causes internal wear.
- Excessive pressure on the system – Leads to overheating and failure.
Diagnosis and Repair:
- Listen for unusual noises like whining or rattling, indicating cavitation.
- Inspect for fluid contamination and replace if necessary.
- Check for leaks in the suction line, which can cause air to enter the system.
- Replace the pump if wear is excessive.
5. Hydraulic Leaks
Leaks are one of the most common issues in tractor hydraulic systems, leading to fluid loss, reduced pressure, and overheating.
Causes:
- Cracked or worn hoses – Result from age, heat, and pressure stress.
- Leaking seals or O-rings – Can dry out and crack over time.
- Loose fittings – Cause slow leaks.
- Excessive system pressure – This can rupture weak components.
Diagnosis and Repair:
- Inspect all hoses and fittings for signs of fluid loss.
- Replace worn-out seals and O-rings.
- Tighten loose fittings to prevent slow leaks.
- Ensure the pressure relief valve is set correctly to avoid excessive system pressure.
Preventive Maintenance Tips for Hydraulic Systems
1. Regular Fluid Checks
- Inspect fluid levels: Check the hydraulic fluid levels daily before operating your equipment. Low fluid levels can cause air to enter the system, leading to decreased performance and potential damage.
- Change hydraulic fluid: Follow the manufacturer's recommendations for hydraulic fluid change intervals. Over time, hydraulic fluid degrades and becomes contaminated, reducing its effectiveness and increasing the risk of component wear.
- Check for contamination: Regularly inspect the hydraulic fluid for signs of contamination, such as water, dirt, or metal particles. Contaminated fluid can cause damage to pumps, valves, and other hydraulic components.
2. Keep Filters and Screens Clean
- Replace hydraulic filters: Adhere to the manufacturer's recommended filter replacement schedule. Filters remove contaminants from the hydraulic fluid, preventing damage to sensitive components.
- Clean suction screens: During fluid changes, clean the suction screens to remove debris that could restrict fluid flow and damage the hydraulic pump.
- Inspect filter bypass valves: Ensure that filter bypass valves are functioning correctly. A faulty bypass valve can allow contaminated fluid to circulate in the system, causing damage.
3. Inspect Hoses and Fittings
- Check for wear and tear: Regularly inspect hydraulic hoses for signs of cracks, bulges, or leaks. Damaged hoses can cause fluid leaks and pressure loss, leading to decreased performance and potential safety hazards.
- Tighten fittings: Ensure that all fittings are tight and leak-free. Loose fittings can cause fluid leaks and pressure loss, leading to decreased performance and potential safety hazards.
- Replace damaged hoses and fittings: Replace any damaged ones promptly to prevent fluid leaks and maintain system pressure.
4. Monitor Temperature
- Avoid overheating: Operating hydraulic systems at high temperatures for extended periods can cause fluid degradation, seal damage, and component wear.
- Check cooling systems: Regularly inspect and maintain the system to ensure it is functioning correctly and prevent overheating.
- Monitor operating temperature: Use a temperature gauge to monitor the hydraulic fluid temperature during operation. If the temperature exceeds the manufacturer's recommended range, stop the operation and investigate the cause.
5. Bleed Air from the System
- Bleed air: If the hydraulic system exhibits erratic performance, such as sluggish operation or jerky movements, bleed air from the system using the manufacturer's recommended procedure.
- Identify the source of air: If air repeatedly enters the system, investigate the cause and repair any leaks or damaged components.
- Prevent air ingress: Ensure that all fittings are tight, hoses are in good condition, and fluid levels are maintained to prevent air from entering the system.
Additional Tips
- Use the correct fluid: Always use the hydraulic fluid specified by the manufacturer. Using the wrong fluid can cause damage to seals, pumps, and other components.
- Store fluid properly: Store hydraulic fluid in a clean, dry, and sealed container to prevent contamination.
- Avoid overfilling: The hydraulic reservoir can cause fluid foaming and decreased system performance.
- Keep the area clean: To prevent contamination of the fluid and components, keep the area around the hydraulic system clean and free of debris.
- Safety procedures: Always follow safety procedures when working on hydraulic systems, including wearing protective gear and using proper lifting techniques.
By following these preventive maintenance tips, you can keep your hydraulic system in top condition, reduce the risk of failures, and extend the life of your equipment.
Conclusion
A well-maintained hydraulic system is essential for a tractor’s performance. Understanding common failure points, diagnosing issues correctly, and applying preventive maintenance can minimize downtime and costly repairs.
If you experience persistent hydraulic issues, consult a professional to prevent further damage to your tractor.
Shop Locations
Fleetworks Inc. is proud to have expanded to three locations across California, providing a wide-range of truck & equipment repair & fleet services from our locations in Oakland, Santa Fe Springs, Riverside, & the surrounding areas.
Santa Fe Springs Location
14011 Marquardt Ave, Santa Fe Springs, CA 90670
Riverside Location
*Equipment Service & Repairs only*
1310 Dodson Way, Riverside CA, 92507