How Technological Advancements Are Changing Heavy-Duty Truck Repair Shops
Discover how technology is transforming heavy-duty truck repair shops. Learn about advanced diagnostics, automation, virtual training, and telematics that improve efficiency, accuracy, and customer satisfaction.
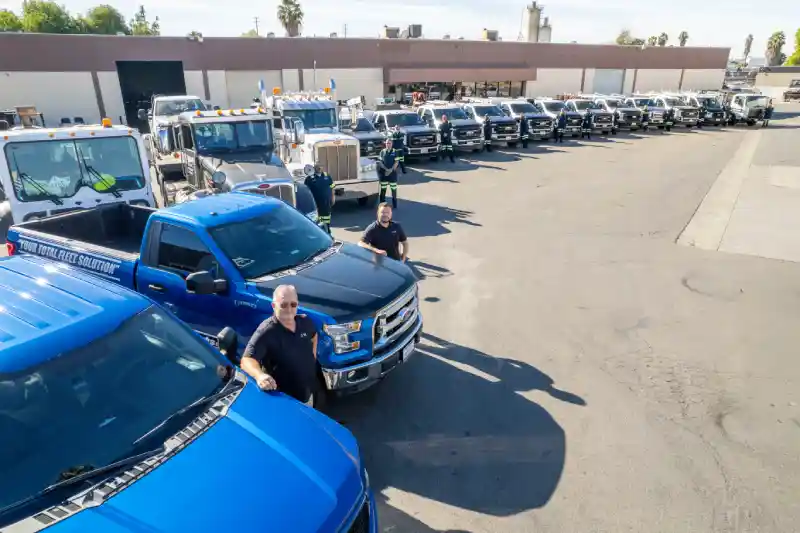
As heavy-duty trucks evolve with cutting-edge technology, repair shops are transforming to keep up. Technology has reshaped what it means to manage a heavy-duty repair shop effectively, from diagnostics and repair tools to communication and data tracking. Here, we explore some of the most significant technological advancements that enhance efficiency, accuracy, and customer satisfaction in heavy-duty truck repair.
1. Advanced Diagnostics and Predictive Maintenance Tools
One of the most impactful changes in heavy-duty truck repair has been the introduction of advanced diagnostics and predictive maintenance technology. Modern diagnostic tools are no longer limited to simple engine scans; they now interface with the complex computer systems in trucks to read multiple electronic control modules (ECMs). This means that shop technicians can pinpoint issues in engines and brakes, transmissions, fuel systems, and exhaust aftertreatment systems.
Predictive Maintenance: This technology has taken diagnostics a step further, allowing shops to foresee problems before they become critical. Predictive maintenance tools monitor vibration levels, temperature fluctuations, and fluid conditions to detect when a component is at risk of failure. With predictive capabilities, repair shops can schedule maintenance at the perfect time, reducing downtime and enhancing fleet efficiency.
2. Automation and Robotics
Automated Equipment: Automated tools, such as robotic lifts, pneumatic tire changers, and advanced alignment machines, have streamlined the repair process. These systems allow shops to handle larger workloads without sacrificing quality, as they reduce the need for manual, labor-intensive work. This is particularly helpful for tasks like wheel alignments, which can now be accomplished faster and more accurately.
Precision Robotics: Precision-focused robotics enable technicians to perform repairs with minimal error, enhancing safety and efficiency. These robotic tools assist with tasks such as torquing bolts, handling large or hazardous components, and consistently executing repetitive tasks, reducing the risk of technician fatigue and error.
3. Digital Documentation and Inventory Management
Gone are the days of keeping shelves of paperwork for each repair job. With digital management systems, heavy-duty truck repair shops now keep a digital footprint of each truck, including service history, parts usage, and recommendations for future work. This provides a seamless record that’s easy for technicians to reference.
Parts and Inventory Tracking: Using RFID (radio-frequency identification) technology and inventory software, shops can automatically track parts as they arrive and are used, helping ensure the necessary parts are on hand when repairs are needed. This integration reduces repair delays due to inventory shortages, and real-time tracking helps shops maintain optimal stock levels.
4. Augmented Reality (AR) and Virtual Training for Technicians
Augmented Reality (AR): AR glasses and applications are increasingly popular in repair shops. By wearing AR devices, technicians can view overlays of repair instructions and diagrams in real-time. This not only speeds up the repair process but also allows technicians to work on complex systems with more confidence. They can also interact virtually with manufacturer support teams or senior technicians remotely, allowing for instant guidance on intricate repairs.
Virtual Training and Simulations: VR-based training has become invaluable for technicians learning to work on newer truck models with unique specifications. These virtual environments replicate real-world repairs and allow technicians to practice before encountering issues on the job. This technology helps train technicians faster and enhances their problem-solving skills without the risk of damaging real equipment.
5. Connected Fleet and Telematics Integration
With telematics, trucks are now more connected than ever. Telematics systems collect vast data on engine health, fuel usage, tire pressure, and driver behavior. Repair shops use this data to gain insights into potential maintenance needs and repair requirements.
Telematics in Real-Time Monitoring: Real-time monitoring enables technicians to observe a truck’s condition remotely. Shops can schedule service appointments based on wear and tear rather than mileage alone. This remote insight into engine diagnostics and performance metrics allows shops to proactively anticipate repairs and order parts.
6. Enhanced Customer Communication and Transparency
Real-Time Updates for Customers: Digital platforms have significantly improved customer experience by enabling real-time communication between repair shops and fleet managers. Customers can now access transparent updates, tracking their truck’s progress throughout the repair process. Many shops also offer digital estimates and invoices, making it convenient for customers to review and approve repairs.
Increased Accountability and Trust: By offering real-time access to the repair process, shops foster trust with fleet managers, as they can see exactly what’s being done on each vehicle. Some shops even provide video or photo documentation of repairs, which can help customers understand complex issues and justify their costs.
Conclusion
The rapid pace of technological advancement is reshaping the heavy-duty truck repair industry. These advancements, from automated diagnostics to virtual training and connected fleet solutions, enable repair shops to operate with higher efficiency, accuracy, and transparency. Embracing these changes positions shops to serve their customers better, streamline operations, and stay ahead of the curve as technology evolves.
Shop Locations
Fleetworks Inc. is proud to have expanded to three locations across California, providing a wide-range of truck & equipment repair & fleet services from our locations in Oakland, Santa Fe Springs, Riverside, & the surrounding areas.
Santa Fe Springs Location
14011 Marquardt Ave, Santa Fe Springs, CA 90670
Riverside Location
*Equipment Service & Repairs only*
1310 Dodson Way, Riverside CA, 92507