Avoiding Diesel Engine Failure: Key Warning Signs & Quick Fixes for Heavy Equipment
Discover the key warning signs of diesel engine failure and quick fixes to keep your heavy equipment running efficiently. Learn how to prevent costly breakdowns.
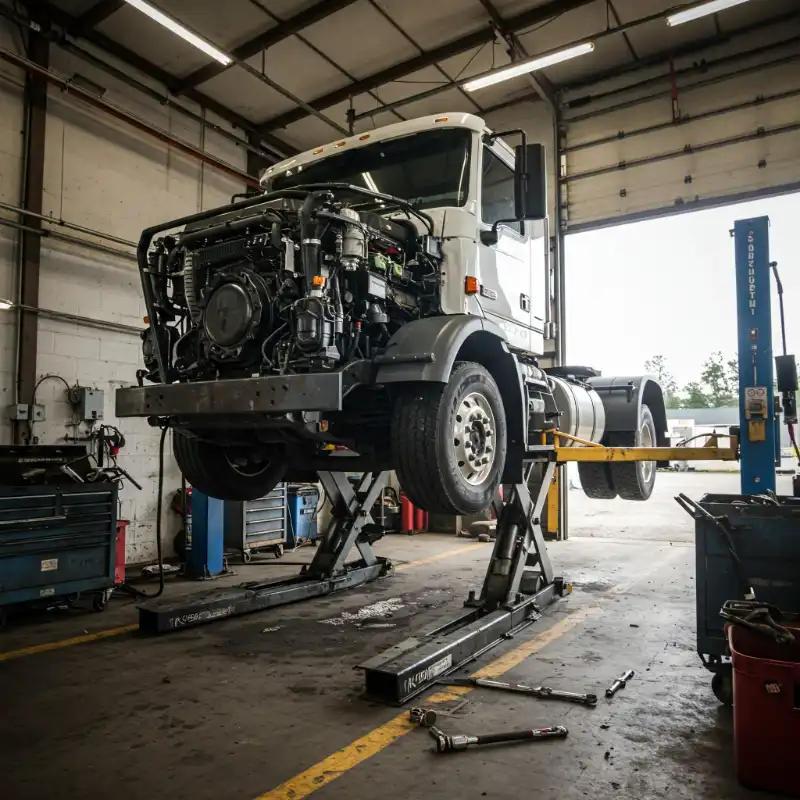
Diesel engines are built to handle extreme conditions but are not immune to wear and tear. Heavy equipment operators depend on these engines to power through demanding tasks, and an unexpected breakdown can mean costly repairs, downtime, and lost productivity. Fortunately, diesel engines often provide warning signs before they fail. Recognizing and addressing these red flags early before they escalate into severe mechanical failures.
This guide will help you identify the most common warning signs of diesel engine failure and provide quick fixes to keep your equipment running smoothly. By staying proactive, you can extend the life of your diesel engine and reduce unnecessary repair costs.
Common Warning Signs of Diesel Engine Failure
1. Excessive Exhaust Smoke
Exhaust smoke is a natural byproduct of diesel combustion, but any excessive amount or change in color can be a red flag for underlying engine problems. The specific color of the smoke can offer valuable clues for diagnosing the root cause:
- Black Smoke signals an overly rich fuel mixture, which means too much fuel is being injected into the combustion chamber. Potential culprits include a malfunctioning fuel injector (which might be delivering too much fuel or leaking), a clogged air filter (restricting airflow and disrupting the fuel-air balance), or a failing turbocharger (impacting air intake and the combustion process).
- White Smoke points towards unburned fuel or coolant in the combustion chamber. This can be due to various issues, such as low compression (resulting from worn piston rings or cylinder walls), glow plug failure (preventing proper fuel ignition), or a head gasket leak (allowing coolant to seep into the combustion chamber).
- Blue Smoke usually indicates that engine oil is burning during combustion. This can stem from worn piston rings (which fail to seal the combustion chamber properly), worn valve seals (allowing oil to enter the cylinder), or a turbocharger oil leak (introducing oil into the intake or exhaust system).
Prompt Action: Key to Prevention
Addressing these issues promptly prevents further engine damage and costly repairs. Here are some potential quick fixes:
- Air Filter Maintenance: Regularly inspect and replace or clean clogged air filters to ensure adequate airflow to the engine. This helps maintain the correct fuel-air ratio and prevents incomplete combustion.
- Fuel Injector Inspection: If black smoke persists, have a qualified technician inspect and replace any faulty fuel injectors. This will restore proper fuel delivery and prevent an overly rich mixture.
- Compression & Coolant System Checks: In cases of white smoke, check for coolant leaks and conduct a compression test to assess the engine's internal condition. Addressing low compression or coolant leaks will prevent further damage and ensure efficient combustion.
- Engine Diagnostics & Repairs: If persistent blue smoke persists, consider having a professional mechanic conduct a thorough engine diagnosis to identify the source of the oil leak. This may involve repairing or replacing worn piston rings, valve seals, or the turbocharger.
Remember, timely maintenance and attention to warning signs like exhaust smoke are essential for keeping your diesel engine running smoothly and maximizing its lifespan. By addressing issues early on, you can avoid major breakdowns, minimize downtime, and optimize the performance and efficiency of your valuable equipment.
2. Hard Starts or No Start Condition
Common causes of a diesel engine not starting include a weak battery, faulty starter motor, malfunctioning fuel pump or injectors, worn-out glow plugs, and a clogged fuel filter. Quick fixes include checking battery voltage, inspecting the starter motor, diagnosing fuel system components, testing glow plug resistance, and replacing a clogged fuel filter. Additional tips include ensuring adequate fuel level, inspecting the air filter, checking for fuel leaks, and considering cold weather effects. Consulting a qualified mechanic is recommended if troubleshooting fails.
3. Loss of Power and Poor Performance
When heavy equipment experiences a noticeable decrease in power or sluggish acceleration, it can often be attributed to several underlying issues within the engine system:
- Dirty or Failing Fuel Injectors: Fuel injectors can become clogged or worn over time, leading to improper fuel atomization and inefficient combustion. This results in reduced power output and sluggish engine response.
- Clogged Air Filter: The air filter prevents dust and debris from entering the engine. A clogged air filter restricts the airflow to the engine, starving it of oxygen and hindering combustion. This leads to a decrease in power and acceleration.
- Turbocharger Failure: The turbocharger increases engine power by forcing more air into the combustion chamber. If the turbocharger fails due to excessive carbon buildup or worn bearings, the engine will lose its boost and experience a significant drop in power and acceleration.
- Low Cylinder Compression: Cylinder compression is crucial for efficient combustion. Worn piston rings, valves, or cylinder walls can lead to low compression, resulting in incomplete combustion and reduced power output.
Addressing these issues promptly is essential to restore engine performance and prevent further damage:
- Cleaning or Replacing Fuel Injectors: Fuel injectors should be cleaned regularly to ensure optimal fuel delivery and combustion. They may need to be replaced if they are excessively worn or damaged.
- Inspecting and Cleaning Air Filters: Air filters should be inspected regularly, cleaned, or replaced to maintain proper engine airflow.
- Checking the Turbocharger: If a turbocharger issue is suspected, it should be inspected for carbon buildup, worn bearings, or other signs of damage. Depending on the severity of the problem, the turbocharger may need to be repaired or replaced.
- Performing a Compression Test: A compression test can diagnose internal engine wear and identify issues like piston rings or valves. If low compression is detected, the engine may need to be rebuilt or overhauled.
4. Overheating Issues
Overheating is one of the most rapid and destructive forces a diesel engine can face. The intense heat can cause warping and distortion of crucial metal components, lead to catastrophic head gasket failures, and ultimately result in complete engine failure. This makes it imperative to understand and address the common causes of overheating:
- Low or leaking coolant: Coolant is vital in regulating engine temperature. When coolant levels are low, or the system is leaking, the engine's ability to dissipate heat is compromised, leading to a dangerous rise in temperature.
- Malfunctioning water pump: The water pump circulates coolant throughout the engine. If it fails due to issues like leaks or worn-out bearings, coolant circulation is disrupted, causing hotspots and overheating.
- Blocked radiator: The radiator acts as a heat exchanger, transferring heat from the coolant to the surrounding air. When the radiator becomes clogged with debris, airflow is restricted, and heat dissipation is hindered, leading to overheating.
- Stuck thermostat: The thermostat regulates coolant flow based on engine temperature. If it becomes stuck in the closed position, coolant is prevented from circulating properly, causing the engine to overheat.
Quick Fixes and Preventative Measures
To avoid the costly and time-consuming consequences of overheating, it's essential to take proactive steps to maintain the cooling system and address any issues promptly:
- Regular coolant checks and top-ups: Check the coolant level regularly and top it off as needed. Inspect the cooling system for any signs of leaks, such as puddles under the vehicle or coolant stains on engine components. If you detect a leak, have it repaired immediately by a qualified mechanic.
- Water pump inspection and maintenance: Periodically inspect the pump for signs of wear and tear, such as leaks, unusual noises, or a loose belt. If you notice any issues, have the water pump repaired or replaced as needed.
- Radiator cleaning and maintenance: Keep the radiator clean and free of debris. If you notice that the radiator is clogged, have it cleaned by a professional or consider replacing it if necessary.
- Thermostat testing and replacement: If you suspect the thermostat is malfunctioning, test it by removing it and placing it in hot water. The thermostat should open at a specific temperature. If it doesn't open or opens at the wrong temperature, replace it with a new one.
Additional Tips
- Use the correct coolant type and concentration: Ensure you're using the coolant type and concentration recommended by the engine manufacturer. Using the wrong coolant or an incorrect concentration can negatively impact the cooling system's performance and lead to overheating.
- Monitor engine temperature: While operating the equipment, keep an eye on the engine temperature gauge. If you notice that the temperature is rising above the normal range, take immediate action to address the issue.
- Avoid overloading the engine: Overloading the engine can cause it to work harder and generate more heat, increasing the risk of overheating. Operate the equipment within its recommended load limits.
- Regular maintenance: Adhere to the manufacturer's recommended maintenance schedule for the cooling system and other engine components. Regular maintenance can help prevent issues that can lead to overheating.
5. Knocking Sounds or Unusual Engine Noises
A diesel engine's normal operation produces a steady and rhythmic sound. Any deviation from this, such as knocking, rattling, or ticking, can be a symptom of underlying issues that require immediate attention. These abnormal sounds often originate from specific components within the engine and can indicate various problems:
- Injector Knock: This sharp, metallic sound occurs when the fuel injector malfunctions, delivering fuel unevenly or at the wrong time. This leads to incomplete combustion and a noticeable knocking noise.
- Rod Knock: A deep knocking sound, often described as a "thunk," indicates worn connecting rod bearings. These bearings connect the pistons to the crankshaft, and excessive play causes a knocking noise when they wear out. If left unaddressed, this is a serious issue that can lead to catastrophic engine failure.
- Valve Train Noise: A ticking or tapping noise often stems from problems within the valve train components, such as worn camshaft lobes, lifters, or rocker arms. This can be due to poor lubrication, excessive wear, or improper valve lash adjustment.
Quick Fixes to Address Engine Noise
Prompt action is crucial to prevent further damage and costly repairs when unusual engine noises occur. Here are some potential solutions:
- Oil Change: Ensuring proper lubrication is essential for engine health. Changing the engine oil and filter can reduce friction and wear, potentially resolving noise issues caused by inadequate lubrication.
- Fuel Injector Inspection and Replacement: If an injector knock is suspected, the fuel injectors should be inspected and tested. Faulty injectors should be replaced to restore fuel delivery and combustion, eliminating the knocking noise.
- Advanced Diagnostics and Repairs: Further investigation is necessary if the knocking persists or is severe. This may involve checking the connecting rod bearings for wear and tear, inspecting the valve train components, and adjusting the valve lash settings. A qualified mechanic with specialized tools and expertise is best suited to perform these tasks.
Ignoring unusual engine noises can lead to severe consequences, including engine damage, decreased performance, and increased fuel consumption. By addressing these issues promptly, you can ensure the longevity and reliability of your diesel engine, preventing costly breakdowns and maximizing its operational life.
6. Oil Pressure Warning or Contaminated Oil
Low oil pressure in a diesel engine is a critical issue caused by worn oil pumps, clogged passages, low oil levels, incorrect oil viscosity, internal leaks, or faulty sensors. Quick fixes include regular oil checks, oil and filter changes, filter inspection, and using the correct oil viscosity. Persistent low pressure requires professional inspection and repair. Addressing low oil pressure promptly is vital to prevent extensive engine damage and ensure longevity.
7. Fuel Efficiency Drops Significantly
A sudden drop in fuel efficiency indicates your diesel engine isn't operating at its peak. This translates to more fuel being consumed to produce the same amount of power, directly impacting your operational costs and potentially leading to more severe engine problems if left unaddressed. Several underlying issues could be causing this decrease in fuel efficiency:
- Clogged or Dirty Fuel Injectors: Over time, carbon deposits can accumulate on the fuel injectors, hindering fuel atomization and disrupting combustion. This results in incomplete combustion, wasted fuel, and reduced power output.
- Malfunctioning Oxygen Sensors: The oxygen sensor is critical in monitoring the oxygen content in the exhaust gases and relaying this information to the engine control unit (ECU). A faulty oxygen sensor can provide inaccurate readings, leading the ECU to miscalculate the air-fuel mixture. This can result in either a rich (too much fuel) or lean (too little fuel) mixture, negatively impacting fuel efficiency and engine performance.
- Turbocharger Failure: The turbocharger boosts engine power and efficiency by forcing more air into the combustion chamber. However, due to worn bearings, damaged seals, or excessive carbon buildup, a failing turbocharger won't deliver the required boost pressure, leading to reduced engine efficiency and increased fuel consumption.
- Air Filter Restriction: A clogged air filter restricts airflow to the engine, starving it of oxygen and causing incomplete combustion. This results in reduced power, increased fuel consumption, and black smoke from the exhaust.
- Exhaust System Blockage: A blockage in the exhaust system, such as a clogged diesel particulate filter (DPF) or a damaged catalytic converter, creates back pressure, hindering the engine's ability to expel exhaust gases efficiently. This reduces engine power and fuel efficiency.
- Low Compression: Worn piston rings, cylinder walls, or valves can lead to low compression, causing incomplete combustion and wasted fuel.
- Incorrect Valve Timing: If the engine's valves are off, the intake and exhaust valves won't open and close at optimal times, affecting the engine's breathing and combustion efficiency.
Quick Fixes to Improve Fuel Efficiency:
- Fuel System Cleaner: A good quality fuel system cleaner can help remove carbon deposits from the fuel injectors, intake valves, and combustion chamber, restoring optimal fuel atomization and combustion.
- Inspect and Clean MAF and Oxygen Sensors: Regularly inspect the mass airflow sensor (MAF) and oxygen sensors for dirt and debris and clean them as needed. If they are faulty, replace them with new ones.
- Check Turbocharger: Inspect the turbocharger for leaks, excessive shaft play, or carbon buildup. If necessary, have it rebuilt or replaced by a qualified technician.
- Replace Air Filter: To ensure proper airflow to the engine, regularly replace the air filter according to the manufacturer's recommendations.
- Inspect Exhaust System: Check the exhaust system for blockages, such as a clogged DPF or a damaged catalytic converter. Have them cleaned or replaced as needed.
- Compression Test: If you suspect low compression, perform a compression test on the engine to determine the cause and extent of the problem.
- Check Valve Timing: If the engine's valve timing is off, have it adjusted by a qualified technician.
Remember that these are just a few potential causes of decreased fuel efficiency in diesel engines. If you're experiencing a sudden drop in fuel efficiency, it's best to consult a qualified diesel mechanic to diagnose the problem and recommend the appropriate repairs. By addressing the underlying issue promptly, you can restore your engine's fuel efficiency, save money on fuel costs, and prevent further engine damage.
Preventative Maintenance to Avoid Diesel Engine Failure
While quick fixes can keep your engine running, preventative maintenance is the best way to avoid costly repairs and unexpected downtime.
- Change oil and filters regularly: Dirty oil increases wear and tear.
- Monitor coolant levels: Prevent overheating by maintaining proper coolant levels and inspecting for leaks.
- Inspect fuel injectors: Clean or replace them periodically to ensure efficient combustion.
- Check the turbocharger: Excessive soot or oil leaks can indicate early failure.
- Monitor exhaust color: Smoke is often the first indicator of engine trouble.
Implementing a regular maintenance schedule can extend the life of your diesel engine, reduce repair costs, and improve fuel efficiency.
Conclusion
Diesel engine failure rarely happens without warning. Operators can identify potential failures early by staying alert to excessive smoke, power loss, overheating, unusual noises, and oil pressure issues. Addressing these warning signs promptly can prevent minor problems from escalating into expensive engine repairs.
Routine preventative maintenance remains the best defense against diesel engine failure. Simple actions like changing oil, monitoring coolant levels, inspecting fuel injectors, and ensuring the turbocharger is functioning correctly can extend the life of your equipment and improve its performance.
Take immediate action if your heavy equipment shows any of these warning signs. The longer you wait, the more severe—and costly—the damage can become.
Shop Locations
Fleetworks Inc. is proud to have expanded to three locations across California, providing a wide-range of truck & equipment repair & fleet services from our locations in Oakland, Santa Fe Springs, Riverside, & the surrounding areas.
Santa Fe Springs Location
14011 Marquardt Ave, Santa Fe Springs, CA 90670
Riverside Location
*Equipment Service & Repairs only*
1310 Dodson Way, Riverside CA, 92507